Projects
The main part of our research projects is conducted in close collaboration with Danish industrial companies and is typically co-granted by public Danish and European funding organisations, industrial partners and DTU. On this page is a selection of our current and completed research projects.
Current projects
Objective
Using a pyrolysis process, plastic can be cracked down to fractions of shorter carbon chains. The highest plastic quality is obtained from the naphtha fraction (C5-C12), which should thus be maximized. It is thought that the formation of the naphtha fraction can be facilitated by use of a catalyst and hydrogen.
The scope of this project is to determine an optimal catalytic reactor configuration for the production of naphtha using both pure plastics and bio-plastic mixtures.
Background
Plastic solid waste (PSW) is a major source of environmental pollution. In an effort to utilize the waste, it is of high interest to recycle the plastics. However, during mechanical recycling, the plastic quality decays for each cycle. This only allows for a few recycles and better alternatives are sought after.
One option is chemical recycling, where the specific carbon chain lenghts that plastics are produced from are targeted.
The project
The project is an experimental investigation of hydropyrolysis of plastics into shorter carbon chain fractions in a catalytic reactor configuration.
The setup consists of both a fluidized bed and a fixed bed, giving four possible configurations, depending on whether or not a catalyst is applied in each bed.
The role of catalyst choice and deactivation will be investigated and reaction conditions will be optimized to maximize the formation of the naphtha (C5-C12) fraction.
For more information, contact:
- Troels Kaas Ibsen, PhD Student, DTU
- Anker Degn Jensen, Professor, DTU
- Martin Høj, Assistant Professor, DTU
Contact
Anker Degn Jensen Professor Department of Chemical and Biochemical Engineering aj@kt.dtu.dk
Contact
Troels Kaas Ibsen Student Students s144190@student.dtu.dk
Contact
Martin Høj Associate Professor Department of Chemical and Biochemical Engineering mh@kt.dtu.dk
Objective
In order to close the plastic recycle loop, CO2 from plastic incineration should be converted back to new plastic.
Background
The unsaturated hydrocarbons ethene, propene, and butenes, collectively called light olefins, and the aromatic molecules benzene, toluene and xylene are the main monomers (or monomer precursors) in the manufacture of plastics. Since light olefins and aromatics are mainly produced from crude oil there is an increasing demand for recycling to make the consumption more sustainable. The best way is direct recycling by melting into new products. However, it has recently become clear that only a fraction of the consumer sorted plastic is possible to recycle directly. Some of the remaining plastic could be chemically recycled (e.g. depolymerization or pyrolysis to a liquid resembling crude oil, see project Bi-cycle), but some plastic will inevitably be incinerated, to avoid it ending up on landfills, which is worst way of handling waste.
The project
This project develops a process for direct conversion of CO2, which could be captured from waste incineration, and H2, which could be obtained from water electrolysis, into light olefins and/or aromatics as plastic monomers or monomer precursors. Combining commercial high or ultra-high temperature water gas shift catalysts with systematically varied, zeolite based methanol to olefins/aromatics catalysts, dual catalyst systems for direct conversion of CO2 to olefins/aromatics will be prepared. These catalyst systems will be evaluated in terms of their structure-activity-selectivity relationship using a flow reactor setup, advanced spectroscopy and electron microscopy. This will enable evaluation of the potential for a process converting CO2 to plastic monomers and lay the foundation for future rational improvements of the catalysts and process conditions.
Independent Research Fund Denmark, Technology and Production Sciences.
For more information, contact:
Martin Høj (Project manager)
Jakob Munkholt Christensen
Michael Thorstein Nikolajsen (PhD student)
Contact
Martin Høj Associate Professor Department of Chemical and Biochemical Engineering mh@kt.dtu.dk
Contact
Jakob Munkholt Christensen Associate Professor Department of Chemical and Biochemical Engineering Phone: +45 45252810 jmc@kt.dtu.dk
Objective
The objective of this project is to develop the MOSAIK technology, for converting sugars into valuable chemicals. A pilot-scale cold flow experimental setup, simulating a dual circulating fluidized bed, will be designed and constructed. Experiments will be performed on the setup to generate hydrodynamic data. A CFD model of the setup will be developed, which will be validated using the obtained experimental data. The CFD model will eventually be scaled up to an industrial sized unit.
Background
Several important chemicals, such as glycolaldehyde, are produced using fossil-based resources. Haldor Topsøe has developed the MOSAIK technology to produce these chemicals in a sustainable manner, where sugar is used as the raw material. This technology has been tested in the lab-scale, and the next step towards commercializing this technology is to scale up, for which hot and cold pilot-scale setups will be built, followed by an industrial-scale unit.
The project
The cold flow experimental setup will simulate the hydrodynamic conditions in a dual circulating fluidized bed. Experimental data obtained from the setup, in the form of pressure profiles, particle velocities and particle concentrations, will help understand the hydrodynamic behaviour of the setup, and improve the design of the eventual industrial-sized unit. The data will also be used to validate a CFD model, to provide further insight into the setup.
The project is funded by Innovationsfonden and is running from 2017 October until 2021
Contact
Anker Degn Jensen Professor Department of Chemical and Biochemical Engineering aj@kt.dtu.dk
Objective
In collaboration with FLSmidth and ROCKWOOL the CHEC group will develop sustainable process technologies that will increase the use of renewable fuels and raw materials and reduce CO2 emissions. The project is funded by Innovation Fund Denmark. The research will include studies on use of alternative fuels in large process plants, optimization of industrial cyclones, development of process technologies for low CO2 ROCKWOOL and cement production and reduction of emissions form building materials production.
Through lower CO2 emissions and reduced fuel consumption, ROCKWOOL expects its production to become more sustainable. For FLSmidth, using alternative cement formulas and production methods will enable the company to launch more efficient technologies for using renewable fuels and reducing emissions.
Background
Both companies use or sell production technologies based on high temperature processes, and the CHEC expertise with respect to measurements in industrial high temperature reactors, reduction of harmful deposit formation, use of alternative fuels and reduction of emissions will be utilized to obtain further understanding of the applied process technologies. This understanding will make a basis for a further development of sustainable building materials production.
The project
Making the production of cement and insulation materials more sustainable will not only benefit the climate, but also strengthen the exports of the Danish building materials industry to global markets. By enhancing energy utilisation, minimizing environmental impact and maintaining high waste recycling rates, these companies will strengthen their essential technological pole position and thus their competitive strength in global markets.
For more information, contact:
Contact
Peter Arendt Jensen Senior Researcher Department of Chemical and Biochemical Engineering Phone: +45 45252849 paj@kt.dtu.dk
Contact
Anne Juul Damø Senior Researcher Department of Chemical and Biochemical Engineering Phone: +45 45252936 ajp@kt.dtu.dk
Contact
Kim Dam-Johansen Professor, Head of Department Department of Chemical and Biochemical Engineering KDJ@kt.dtu.dk
The scope of this project is to explore the feasibility of using waste plastics to reduce nitrogen oxides (NOx) emissions from industrial combustion processes through the reburning technology. Experiments and modeling studies will be performed to understand the reburning process of waste plastics.
As a global environmental issue, the accumulation of waste plastics is as concerning as the NOx emissions from anthropogenic sources. With fuel reburning being an important NOx reduction technology, the utilization of waste plastics as the reburning fuel can be an environmentally friendly process reducing simultaneously the amount of waste plastics and NOx emissions. The hydrocarbon-rich fragments of some plastics are expected to be favorable for reducing NOx during the reburning process, but limited knowledge on this topic is available. The aim of this project is thus to investigate the NOx reduction efficiency of waste plastics during the reburning process.
Reburning experiments using various types of plastics will be performed on a fixed bed reactor and an entrained flow reactor to determine NOx reduction efficiency and explore optimal conditions for the process. Additionally, chemical kinetic modeling will be carried out to understand the reactions of NOx and plastics under reburning conditions. By exploring the feasibility of plastic waste reburning for NOx reduction and by evaluating the optimal operation conditions, this project can help to facilitate the sustainable utilization of waste plastics in industrial reburning processes.
The project is funded by Villum Experiment and runs from 1 January 2021 - 31 December 2022.
For more info, contact:
- Hao Wu (Project manager)
- Yifan Du (Postdoc)
Contact
Hao Wu Professor Department of Chemical and Biochemical Engineering Phone: +45 45252927 haw@kt.dtu.dk
Objective
The goal of WOODI is to develop a predictive model for the dissolution rate of mineral wool fibres as a function of fibre and solution composition. Of particular interest is pH promoted dissolution (product stability) and organic acid promoted dissolution (biosolubility).
Background
Stone wool products such as insulation, can dissolve partially or fully when in contact with a solution. For loose fibres inhaled during construction, dissolution in the lungs is desired (biosolubility) and is key in the safety profile of the product. For applications where stone wool e.g. is in direct contact with the ground, resistance to dissolution is directly related to product stability. A fundamental understanding of the dissolution process can help future product design.
The project
The dissolution will be modelled using a microkinetic model, which in turn will be based on molecular scale properties of the fibre surfaces. The required proerties include surface chemistry as a function of pH and solution additives as well as the dissolution barriers for the various components of the material. We will be using a combination of computational chemistry and key experiments to build the model.
The project is funded by ROCKWOOL A/S
Contact
Wolfgang Stelte Senior Researcher Department of Chemical and Biochemical Engineering wost@kt.dtu.dk
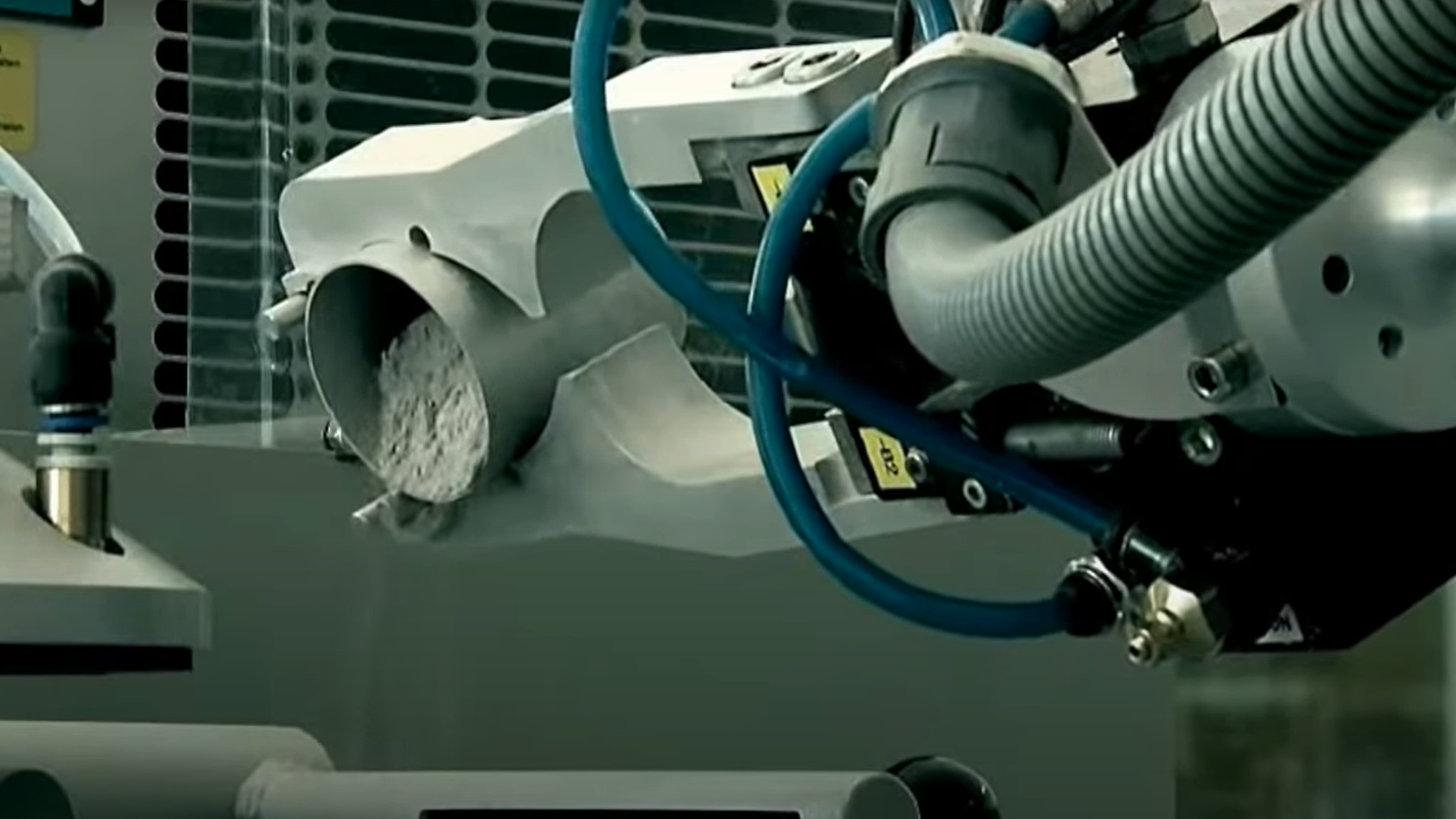