Coating formulation and production principles
Coating production has always been batch production in which the pigment dispersion takes place. However, new in-line dispersion and formulation principles make the production more effective.
In-line dispersion principles
Traditionally, coating production has always been batch production in which the pigment dispersion takes place. However, new in-line dispersion principles have recently been introduced making it possible to transform from batch to semi-continuous mode. The aim is to convert to full-continuous mode in the future.
The dispersion of pigments into the coating binder phase is one of the most critical unit operations in coating production. When pigments are manufactured, the individual particles will be present in porous agglomerates due to physical interactions. During the subsequent coating production, these agglomerates need to be taken apart into smaller units to provide the right properties to the coating.
This dispersion process is complex and consists of three separate steps: wetting of pigments, breakage of agglomerates and stabilization of the primary particles. Depending on the type and purpose of the pigment, the dispersion techniques may vary.
The in-line mixers seem so far to be very efficient on many types of pigments; however, more research on the dispersion mechanisms is needed to be able to work on all types of pigment agglomerates. The in-line mixers also make it more feasible to benefit from paint production via intermediate products in modular manufacture.
Disciplines involved in efficient coating production are chemical process technology, chemical unit operations and chemical/physical analytical techniques.
- The coatings society needs new and more efficient production principles
- The aim of this research is to get a better understanding of pigment dispersion and transfer this knowledge to coating production
- The research is performed by combination of theoretical studies, mathematical modelling, dispersion analysis and coating production in modern in-line mixer
Projects
Summary
Modular paint production targets more efficient processes by creating intermediates as building blocks for the final products. By doing so, unnecessary logistics, labor force, and cleaning time can be decreased, and less energy usage can be achieved by optimizing the dispersion processes. For each intermediate, target-oriented solutions for process optimization and quality control methods can be developed. This project aims to explore and optimize modular paint production and facilitate the moving journey towards it.Background
In traditional paint production raw materials are turned into end-products after a set of unit processes. In modular productions, instead of going directly to the end-product, intermediates are created, and end-products are produced with these intermediates. The intermediates might include pigment slurries, filler slurries, additive solutions and/or binder solutions.
Benefits
Changing conventional paint production to modular production with intermediates including in-line production equipment may be more advantageous in terms of energy, material handling and manpower use.
Modular paint production might have significant advantages:
• Powder handling is easier.
• The number of challenging processes such as pigment dispersion is less.
• Shorter production times and less energy use are expected.
• There are opportunities for developing smart solutions, do it yourself products and specialized production facilities or factories.
Method In the laboratory, a pilot study case to compare factory operations running with conventional and modular production system will be performed. Various dispersion methods including in-line disperser will be tested. Performance parameters such as production times and energy will be measured.
Sub-projects
In scope of this project, there will be special focus on some of the intermediates and quality control methods.
• Pigment Wetting: Poor wetting causes harder particle size reduction and poor stabilization. Alternative pretreatment methods (physical, chemical, physiochemical, electrochemical, thermal, etc.) of pigments will be studied to reduce the mechanical power used in pigment dispersion.
• Activation of Rheology Modifiers: Rheology modifiers are used to control flow behavior; so leveling, sagging, settling or thixotropy can be monitored. Some rheology modifiers require activation. The activation mechanism of these materials will be studied to reduce the energy and the amount of rheology modifiers. • Measurement of Fineness of Grind: Fineness of grind is among the most common quality control for pigment dispersions. Traditional grindometer method has major drawbacks. An alternative novel method to measure fineness of grind continuously and objectively will be developed.
Funding
The Hempel Foundation and the Technical University of Denmark (DTU). The project runs from 1 August 2022 - 31 July 2025.
Supervisors
Kim Dam-Johansen
Contact
Bugra Ogla Research Assistant Department of Chemical and Biochemical Engineering bugog@kt.dtu.dk
Contact
Kim Dam-Johansen Professor, Head of Department Department of Chemical and Biochemical Engineering KDJ@kt.dtu.dk
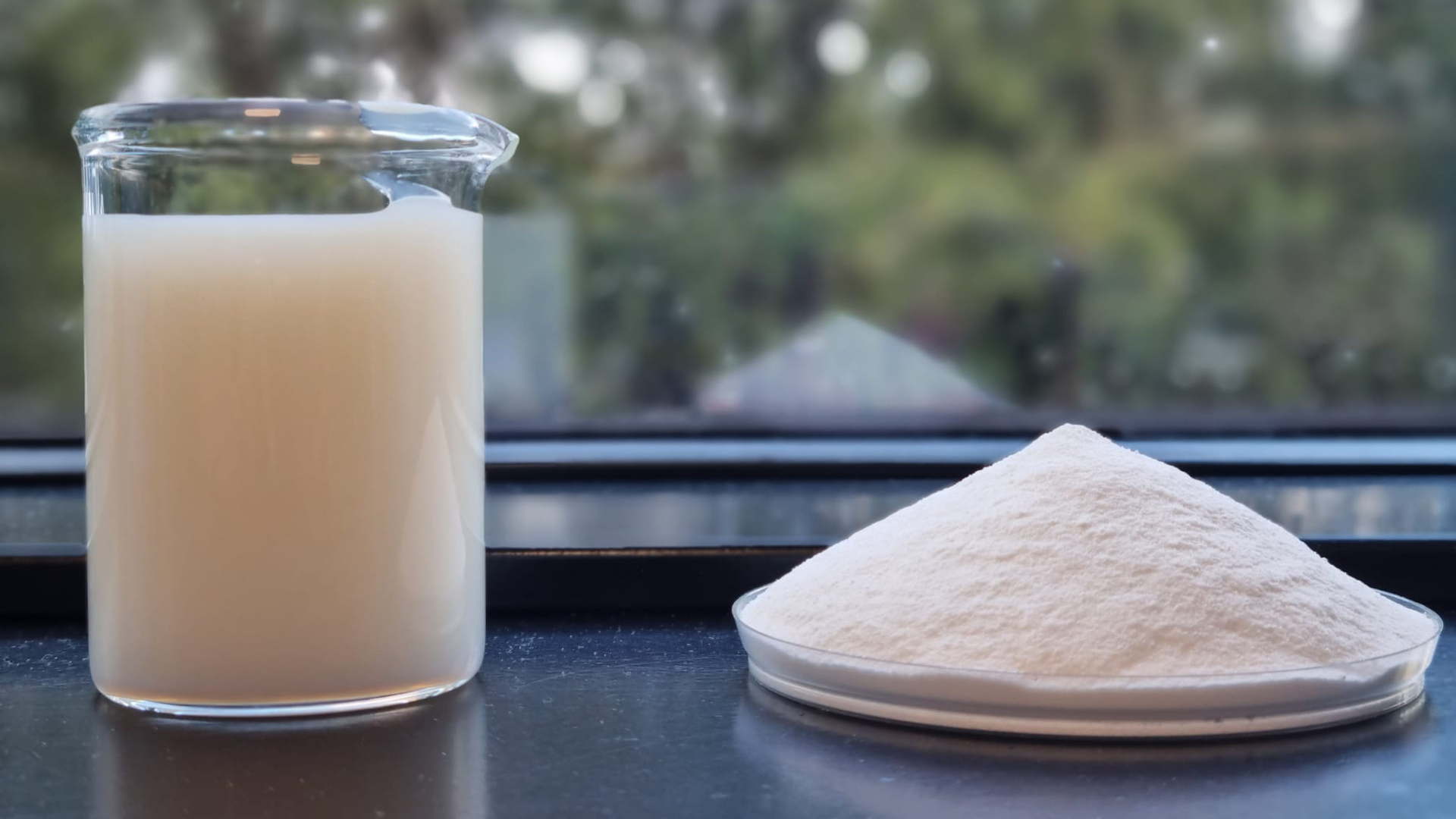
The transition from solventborne coatings to waterborne coatings brought many advantages. But is there a way to make it even better—more cost-effective, sustainable, and regulation-free? This project focuses on eliminating the water content and exploiting the advantages it brings along the supply chain.
Waterborne paints and polymer dispersions are produced, transported, stored and sold in water as solvent. In fact, approximately half of the can is usually water. Because there is water in the container, biocides are also added to stop microbial growth. Therefore, eliminating the water content along the supply chain would provide great benefits including,
- Decreased transportation and storage costs,
- Removal of biocides (which is getting more strictly controlled by the regulations),
- Reduced waste,
- Label-free products.
The main aim of the project is to transform the polymer dispersions into powder form, the so-called Re-dispersible Polymer Powders, by utilizing well-known drying processes. Ideal powders should be capable of reforming the original dispersion when mixed with water, without sacrificing any of the original properties.
Funding
The Hempel Foundation and the Technical University of Denmark (DTU). The project runs from 1 December 2021 - 30 November 2024.
Supervisors
- Kim Dam-Johansen
- Søren Kiil
- Narayanan Rajagopalan
Contact
Okan Aggez Student Students s220398@student.dtu.dk
Contact
Kim Dam-Johansen Professor, Head of Department Department of Chemical and Biochemical Engineering KDJ@kt.dtu.dk